
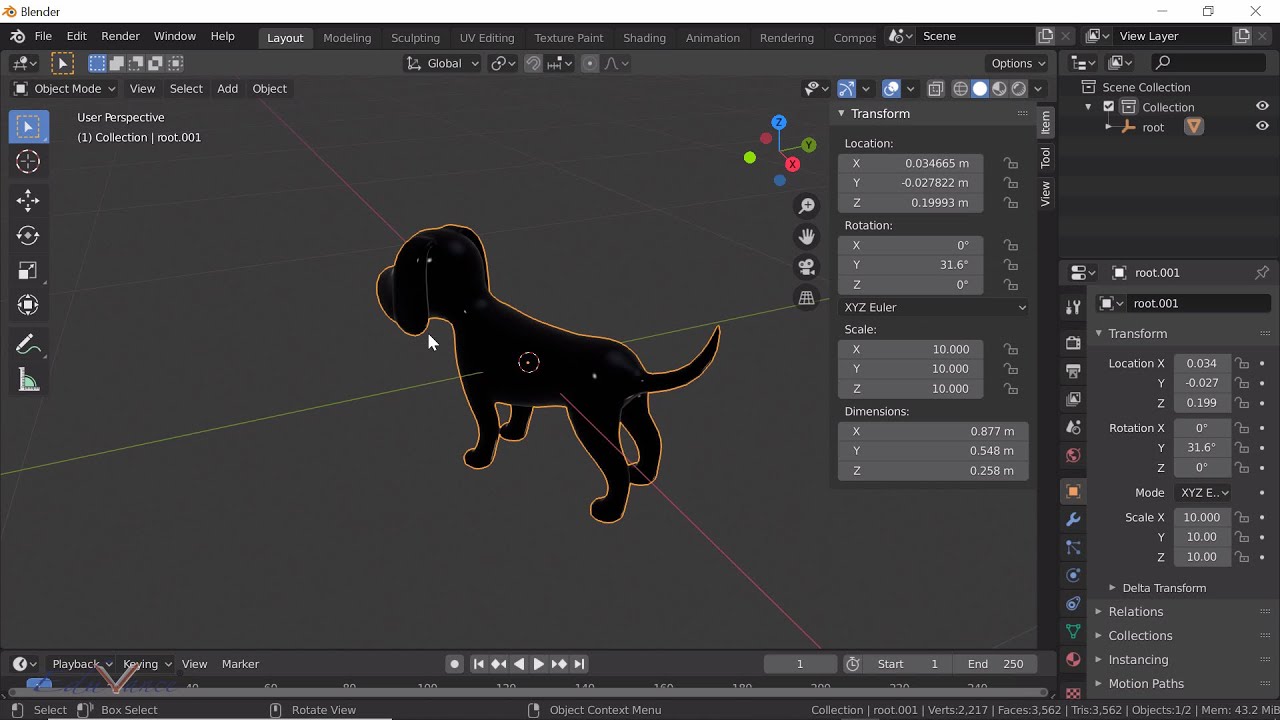

Assign materials, colors, and surface finish to the model.View cross sections of your model so you can ensure no unexpected pockets exist.Scale and position the model on the build platform for the most efficient manufacturing.Identify printability problems within your design, such as narrow gaps and thin walls.Connect and define settings for multiple printers.But these days, you can use a single environment to design, optimize, prepare, and validate designs for 3D printing.
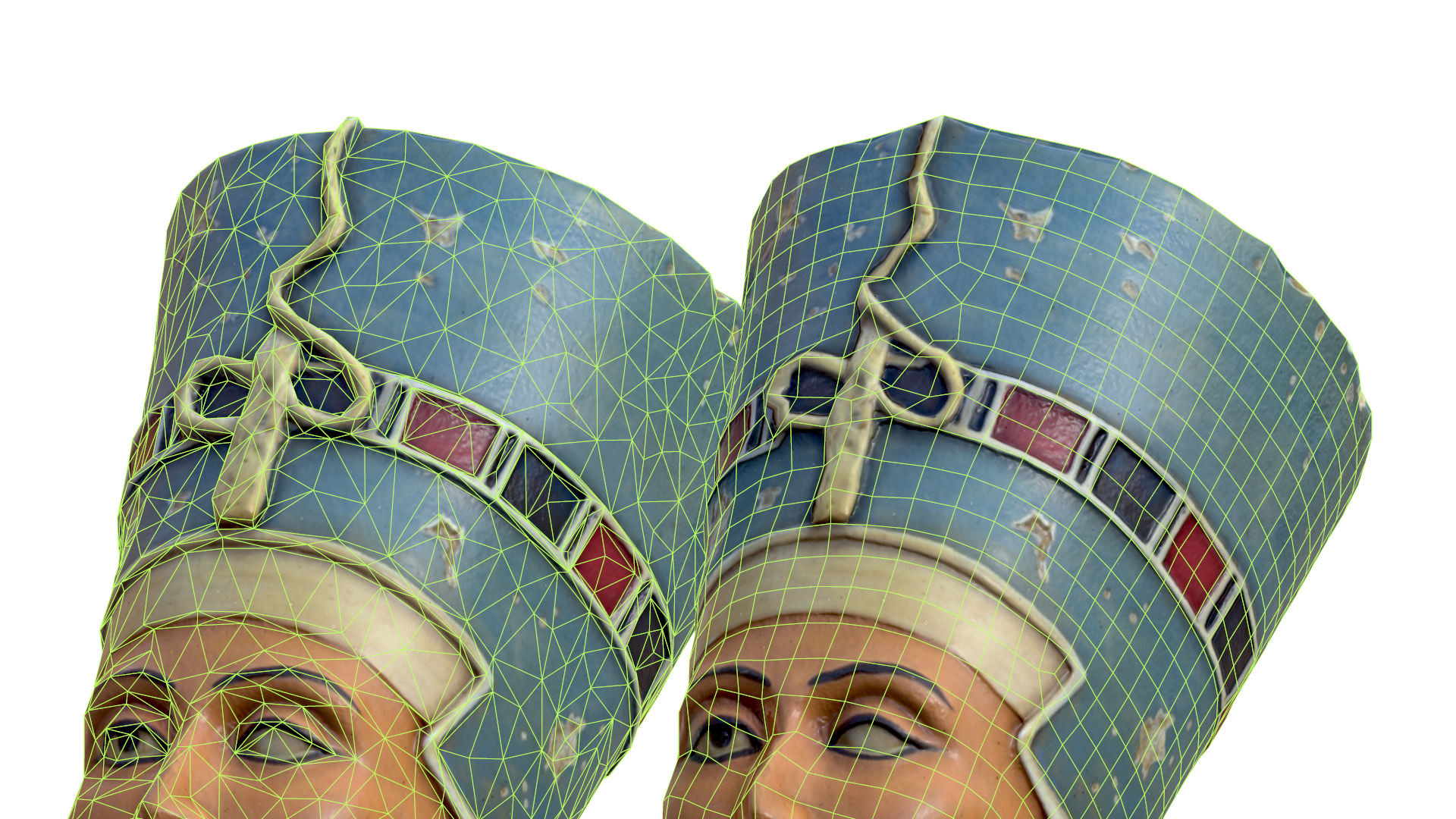
In the past, designers exported their models to various tools for optimization checks. And engineers might also want to set parameters like resolution, finish, and colors before saving the final STL file or sending it to the printer. The physical printer tray introduces some design constraints, too, limiting the size of the model that can be printed. For example, will support material fill cavities too small to clear away in post-processing? They also need to know how the support material will interact with the design.

In this case, a wall is unacceptably thin and probably won’t survive post processing steps once printed.Īs engineers design products that will be manufactured via 3D printing, they need to know whether the model will survive the printing process without breaking-especially during steps like cleaning and polishing. But with all these new options come new requirements for modeling.Ĭreo now includes tools for validating models for 3D printing. With 3D printing (or more correctly, additive manufacturing), product developers have new options for prototyping, tooling, sourcing, and even producing parts.
